Understanding Gears: Essential Components in Mechanical Systems
Gears are fundamental components in a wide range of mechanical systems, playing a crucial role in transmitting power and motion between parts. These toothed wheels can vary in shape, size, and application, but their primary function remains consistent: to transfer torque efficiently and accurately. Whether in industrial machinery, automotive systems, or household appliances, gears are indispensable. In this article, we will explore what gears are, how they work, and their various applications. Additionally, we will touch on the role of geonets in related industries.
What are the different types of gears?
There are several types of gears, each designed for specific applications and functions:
- Spur Gears: The most common type, with straight teeth parallel to the axis of rotation. They are used in simple machines and devices where high speed and power transmission are required.
- Helical Gears: These have angled teeth that gradually engage, providing smoother and quieter operation. They are often used in automotive transmissions and heavy machinery.
- Bevel Gears: These gears have conical shapes and are used to transmit motion between intersecting shafts. They are commonly found in differential drives and various industrial equipment.
- Worm Gears: Consisting of a worm (screw) and a worm wheel, these gears provide high torque with low speed. They are used in lifting mechanisms and conveyor systems.
- Planetary Gears: This complex system involves a central sun gear, planet gears, and a ring gear, allowing for high torque in a compact design. They are commonly used in automatic transmissions.
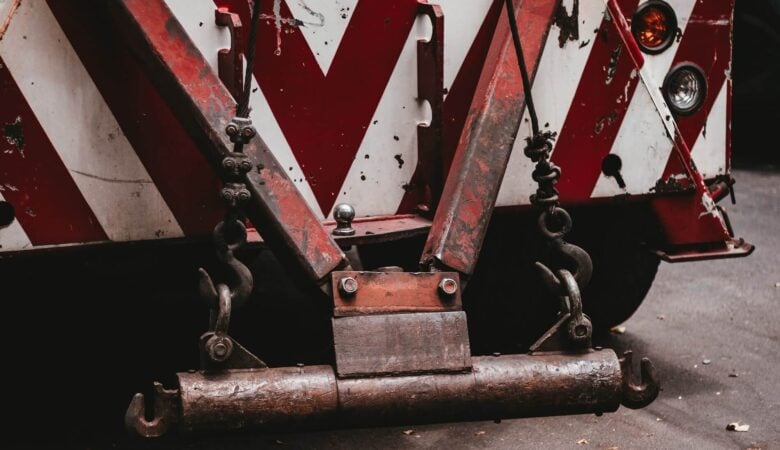
How do gears work in mechanical systems?
Gears function by meshing their teeth together, allowing one gear to turn another. This interaction transfers motion and force from one part of a machine to another, often changing the direction of rotation or increasing torque. The gear ratio, determined by the number of teeth on each gear, plays a key role in how the power is transmitted. For example, a larger gear driving a smaller gear increases speed but reduces torque, while the opposite setup increases torque but reduces speed.
What materials are gears typically made from?
Gears are made from a variety of materials, depending on the application and the demands of the system:
- Steel: Most commonly used for gears due to its strength and durability. It’s ideal for high-load applications such as automotive and industrial machinery.
- Brass: Known for its good machinability and corrosion resistance, brass is used in low-load applications like clocks and small instruments.
- Plastic: Lightweight and resistant to corrosion, plastic gears are used in low-stress applications such as household appliances and toys.
- Cast Iron: Often used in heavy machinery due to its wear resistance and ability to dampen vibrations.
- Aluminum: Lightweight and with good corrosion resistance, aluminum gears are used in applications where weight is a concern, such as in aerospace.
How do geonets relate to gear systems?
Geonets, though primarily used in civil engineering for soil stabilization and drainage, share a commonality with gear systems in terms of their function within larger systems. Just as gears work within machines to ensure proper function and efficiency, geonets are integral in ensuring the stability and longevity of construction projects. In some specialized engineering applications, geonets are used to reinforce the ground beneath heavy machinery, ensuring that the gears and other mechanical components operate on a stable foundation.
Gears are vital components in mechanical systems, enabling the efficient transfer of power and motion. Understanding the different types of gears, their functions, and the materials they are made from can provide insight into their crucial roles across various industries. Additionally, the mention of geonets highlights the interconnectedness of mechanical systems and civil engineering solutions, particularly in maintaining the stability and functionality of machinery in challenging environments. Whether in industrial applications, automotive systems, or other machinery, gears continue to be indispensable to modern technology.